First-generation industrial blue lasers based on semiconductor laser-diode technology were first introduced in 2017. Since then, these lasers became well established primarily for copper and aluminum applications such as welding and 3D printing, which benefitted from the increased absorption vs. infrared (IR) lasers. Even so, the brightness of these lasers still did not meet the requirements for use with industrial 2D galvo scanning systems that are used in many materials processing solutions. With the introduction of a second-generation industrial blue laser, NUBURU has achieved a breakthrough in the design and manufacture of these lasers that now allow their use with industrial 2D scanning systems (see Fig. 1).
This breakthrough is based on an advanced manufacturing process that results in a laser beam with a much smaller spot size and divergence angle. For reflective metal processing applications like welding and 3D printing, the laser beam is often characterized by its brightness or beam parameter product (BPP), which is defined as the product of beam radius (measured at the beam waist) and the beam divergence half angle. The second-generation 450 nm blue laser module is now available with either 125 or 250 W and a BPP of less than 5 mm*mrad— representing nearly a 2X increase in power and a 3X improvement in BPP compared to the first-generation laser module. This generation is also more compact, more reliable, and designed for power scalability. Prisms For Sale
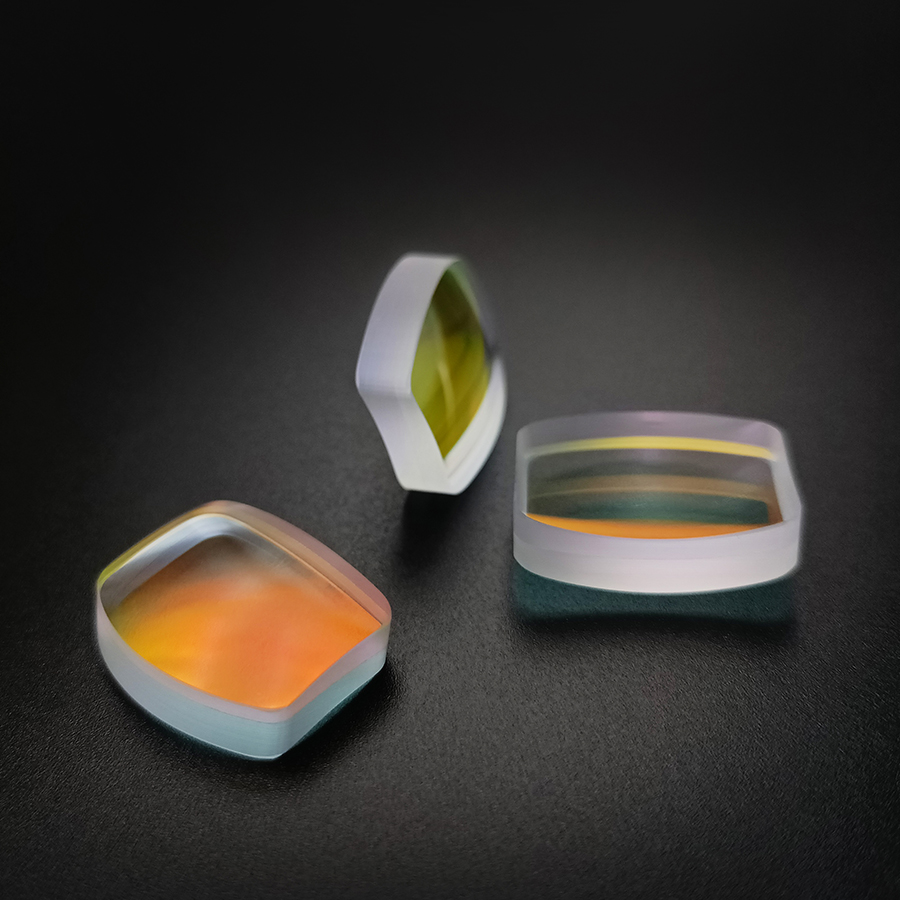
Most importantly, the level of brightness is now sufficient to integrate with industrial scanning systems to open the door for wider adoption of the technology across a range of applications.
NUBURU’s first-generation laser system used pre-packaged semiconductor laser-diode linear arrays that were manually assembled on a module backplane. Each individual laser diode light was then collimated via fast- and slow-axis lenses. The process produced laser modules with 150 W of power and a BPP of 15 mm*mrad.
The changes start at the laser device level. First-generation systems used pre-packaged laser diode linear arrays, while second-generation systems feature individual laser devices in a chip-on-submount (COS) configuration. Moving to individual laser diodes has the advantage of allowing each laser to be driven individually vs. driving the linear laser array. In the linear array, if a single diode fails, the entire array goes offline, and it can lead to a noticeable drop in laser power. In the new design, if a single laser fails, the drop in light output is minimal. This is also a benefit for overall system reliability.
With Gen 1 laser arrays, the positioning and packaging was predetermined, and these arrays were manually placed on the driving backplane. In Gen 2 modules, an automated pick-and-place machine is used to position each device in a tighter configuration. This more precise registration helps preserve the aggregate brightness.
The next step is to attach microlenses to each laser diode. These lenses take the very asymmetric laser output profile to create a collimated beam profile. In Gen 1 modules, these were semi-manually placed and secured. In Gen 2 modules, they are robotically placed and secured in place in a dynamic way. That is, the light output is actively monitored with the position and rotation of each lens optimized for aggregate beam performance. This automation-assisted positioning and lens placement is a key reason the BPP is improved in Gen 2 modules.
The new COS base design offers significant improvements. Perhaps the most impressive aspect is the brightness or BPP performance. For welding and 3D printing applications, it is important to optimize power density defined as the power divided by beam area at the workpiece. The beam diameter at the workpiece is directly related to its divergence (BPP), but optimizing beam divergence offers more bang for the buck. Why? Because power density scales linearly with power, but by a power of 2 for BPP. As a result, while the increase in power from Gen 1 to Gen 2 modules (150 to 250 W) is impressive, the improvement in BPP is even more impressive (from 15 to 5 mm*mrad).
The Gen 2 manufacturing process also enables a much more compact laser module. This is possible because of the flexibility in the close packing of the laser diodes and tight integration of the collection microlenses. The Gen 2 laser module size is about one-tenth the volume of Gen 1 modules.
The new process also has benefits for laser reliability. By controlling every step of the subcomponent preparation and handling in a Class 1000 cleanroom, contamination controls are consistently applied. And robotic assembly leads to a more consistent manufacturing process, with fewer opportunities for operator-induced error. Most importantly, robotics enable a scalable, reproducible process for ramping production capacity.
The performance improvements are significant with a 3X increase in brightness and 2X improvement in power over first-generation lasers. As a result, it enables new integrations with industrial scanning systems for laser welding and laser-assisted additive manufacturing.
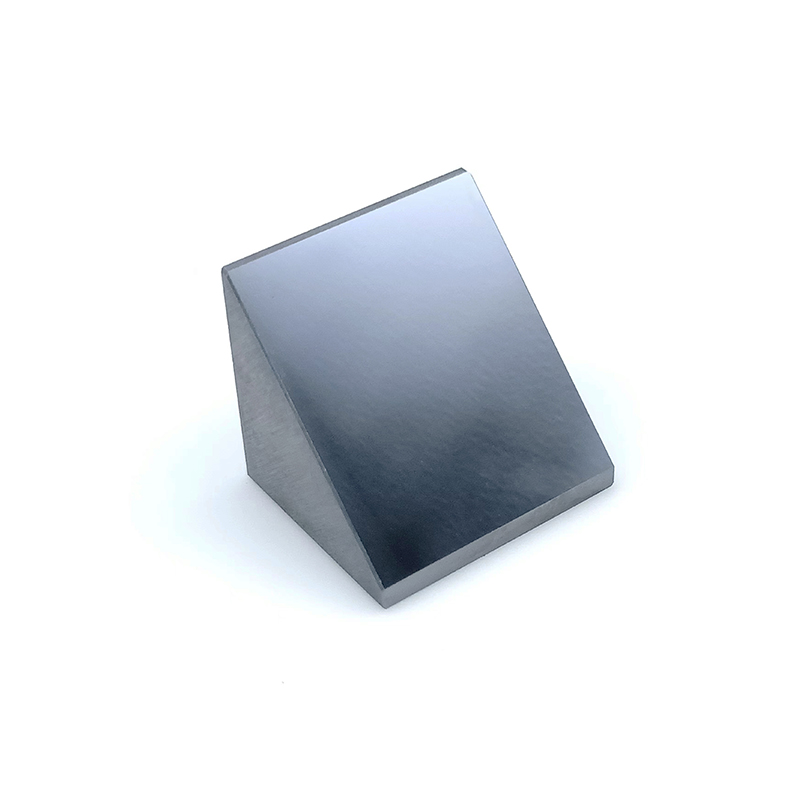
Baf2 Window Dr. Matthew Philpott is chief marketing and sales officer at NUBURU (Centennial, CO). He has 22 years’ experience in the laser industry, most recently focusing on the electric vehicle market for Coherent. He led a multi-year global team effort to grow Coherent’s business, making it one of the top suppliers of lasers for battery manufacturing. Beyond success in the EV market, he has held a wide range of roles in sales, marketing, and business development, with expertise in materials processing, microelectronics, display, and bioinstrumentation. Dr. Philpott holds a B.S. in chemistry and a Ph.D. from the University of Washington in physical chemistry.