MCLOUGHLIN POINT, BC, CANADA -- As the new wastewater treatment plant here reaches the final construction phase, its new outfall pipeline with a diameter so large that a person can stand inside has already been completed. The nearly 2,214 m (1.4 mile) long continuous pipeline is being highlighted in the industry for its use of AGRU XXL 2.25 m (7.4 foot) diameter, high-density polyethylene (HDPE) pipe from AGRU America, Inc. (Georgetown, S.C.). It is the largest pressure pipeline project to date in North America, and the largest solid wall HDPE pressure pipe in North America to be fusion welded.
The Capital Region District in British Columbia has 13 municipalities that joined together to build a new tertiary wastewater treatment plant that would help protect and maintain local waterways. The $775 million project includes a new wastewater treatment facility, outfall system, and residual treatment facility. The design for the HDPE outfall pipe, which will be responsible for discharging the tertiary-treated effluent, called for the ability to handle high-volume flow of 430 megaliters. Viking Johnson Dismantling Joint

The reduced weight of HDPE pipe as compared with concrete and steel pipes of the same size category provided significant cost savings for the client. The pipe’s light weight, durability, and flexibility as well as its ability to be fusion welded contributed to reduced installation time and labor.
The SDR21/SDR26 HDPE pipe was extruded at AGRU’s newest facility located in Georgetown, South Carolina. Additionally, 110 pipe joints, ballast weights, fittings, and custom-fabricated assembly pieces were transported to the site to support the ‘float and sink’ installation of the pipe nearly 200 feet under water. The pipe and supporting pieces were transported by flatbed truck with braces, caps, and saddle-style dunnage for the deck provided by AGRU. ISCO Industries (Louisville, KY), the global piping solutions distributor provided the logistics plan and also the qualified technicians to heat fuse the pipe sections and fittings. The installation was completed in less than 30 days.
Originally, the plan called for steel pipe, which was later upgraded to the AGRU XXL HDPE pipe to meet new design requirements. The pipe’s use of HDPE was cited as a primary benefit—providing increased flexibility, durability, and longevity over competing products of the same size category. The move to HDPE also predicated on the creation of specialized fittings such as the Diffuser Pipe Section and the flange coupling adapter that would connect the HDPE pipe to a steel pipe section. Both fittings, developed with support by ISCO, met design requirements and enabled the project to move forward. By sourcing the pipe and all associated fitting components from AGRU, the designer ensured interoperability and improved the outcome of the installation.
“The CRD Wastewater Treatment Project shows the benefits and a practical application of supersized HDPE pipe,” observed David Fink, president of PPI. “The success of this project will encourage other municipalities to reevaluate their wastewater treatment system, and consider HDPE pipe for their projects, both small and extremely large.”
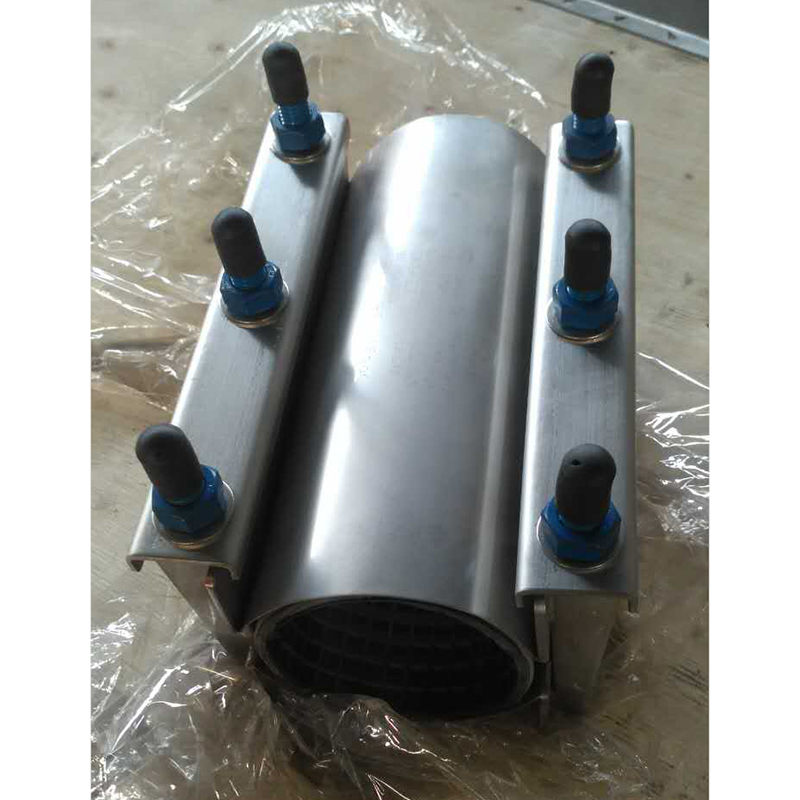
Spigot Joint SOURCE: The Plastics Pipe Institute, Inc. (PPI)