Over the last century, upgrades and developments in thermoplastic valve and piping systems have been installed in a growing range of industries. Actuators, which play an important role in automating these systems, have evolved into smaller and more efficient units since the torque requirements to operate these valves have dropped.
Advancements in actuation have improved the size and reduced the cost of these systems, while also providing more reliable control options. These improvements have contributed to the efficiency of both the most advanced fully automated systems that use data communication protocols and even the simplest remote shutoff valves. Dc Motorized Ball Valve
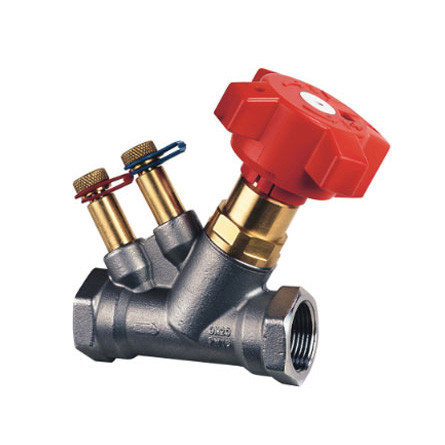
Selecting an actuator for a system typically starts with the power source that is available to control the unit. Actuators usually use one of two methods for power creation: pneumatic or electric inputs. Pneumatic actuators use a simple piston arrangement to turn a compressed liquid or gas into rotatory torque output. The most basic forms of pneumatic pistons are rack and pinions and scotch yoke designs. Scotch yokes are typically cheaper for a bigger torque output but have a nonlinear function of stroke, which is a major difference when compared to rack and pinion design. Rack and pinion actuators can have a smaller frame, and they control positional inputs more efficiently due to their constant torque output. Pneumatic actuators are ideal for applications that need to be immediately operated, given that cycle times are under a second for most valve sizes. An example of a system that may benefit from faster cycle times is an emergency overflow tank that needs quick outlet lines to open up to avoid flooding a designated area.
Electric actuators take a defined voltage signal to power a motor that will give the desired rotary torque. Electric actuators typically fall into brushed or brushless motors that can either run unidirectionally or be reversing. Brushless actuators run more efficiently and have longer life spans, but can be more expensive. Similarly, reversing motors are more versatile in what valves they can operate, but also end up being more expensive to produce.
Quarter turn actuation is the most common form of automation because most valves only need 90 degrees of travel for a full stroke. Simple shut-off or isolation valves can be added to a system to make maintenance downstream easier or add a level of security to a system if an emergency shut down was needed. For smaller system lines, ball valves are used, while butterfly valves typically handle larger pipe sizes. These valves can be seen all over most plumbing systems, ranging from water treatment plants to mining systems and to aquatic life support systems. Any system that needs to be turned off at some point can use these valves. Additional levels of security can be added to these actuated valves by including a mechanical or electric failsafe option to the actuator.
Mechanical fail safes usually incorporate a spring to either the piston of a pneumatic actuator or the gearing of an electrical actuator to physically force the valve to a determined fail position when the power supply is lost to the actuator. Electrical fail safes typically use batteries or capacitors to store power that can be used to electrically operate the valve for at least one cycle to move the valve to a fail position when the actuator loses power.
Multiturn valves, like gate valves, diaphragm valves, needle valves and globe valves, all add a higher degree of control due to longer stroke travel. These valves can all be proportionally controlled with an analog input control signal, like a 4-20 milliamp (mA) signal, to adjust the flow coefficient downstream of a valve. These levels of precision actuators can be synchronized with field devices that measure fluid conditions, like chemical concentrations or water levels in a tank, to fully automate processes. For example, some applications include chemical feeding systems or chlorinated pool concentrations. Larger-scale, multiturn valves typically use electropneumatic positioners, since the electric actuators can take multiple minutes to fully open or close. However, compressed air is not always readily available in all situations. As electric actuators continue to get faster and more efficient, they should become more prevalent in future markets.
Whether there is a single valve in a hard-to-reach location or a full factory setup that needs to be fully automated, actuators help make processes more efficient. Not every job requires the most complicated setup to benefit from automation; so, it is important to identify what types of automation are possible at a site and what level of control and accuracy is needed for the process.

Motorised Valves Zachary Lehmann is a valve and actuation application engineer at Asahi/America. He may be reached at zlehmann@asahi-america.com or 781-388-4569. For more information, visit asahi-america.com.