Part I of this series ran in the June 2023 issue of Pumps & Systems.
With an understanding of bearing design choices, we can now investigate lubrication delivery methods that will ensure an adequate supply of oil to the bearing. The most common methods for oil delivery are ring oiling and circulation oiling. Oil grooving is also used to deliver lubricants across the bearing system. Bearing systems run at maximum efficiency when proper delivery and dispersal are achieved. Stainless Steel Bearings For Nutribullet
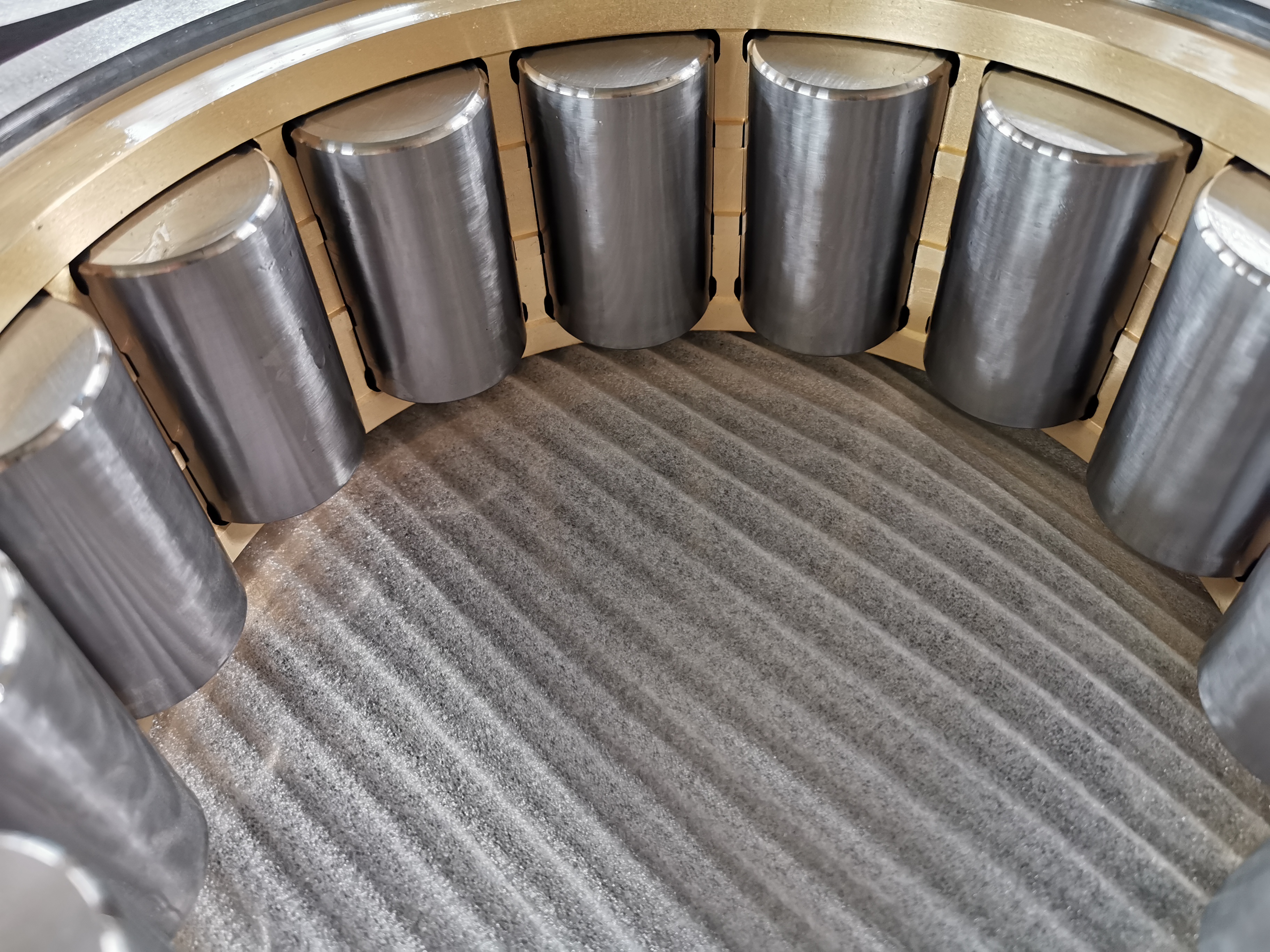
Oil delivered from a central reservoir is often referred to as a circulation system. This reservoir will often supply oil to all bearings in the system. All oil drains back to this reservoir for recirculation. As the supply oil is recirculated, it should go through a filtering and cooling system. Oil can be supplied directly to the bearings with a pressure feed system or by a gravity feed system. For gravity fed systems, oil is pumped into an overhead tank for dispersal back through the system and uses the same methodology to return the oil to the main reservoir. For pressure feed systems, oil is pumped directly into the bearing housing and allowed to gravity feed back into the reservoir main. The flow of oil is often determined by what is required to keep the bearing within acceptable operating temperatures. This amount is more than adequate to create the fluid film required for hydrodynamic operation. As oil is pulled from the reservoir, it should pass through a filter to remove any potential particulate matter that can cause scoring on the shaft journal and bearing lining. Oil coolers are often installed into these systems to regulate input oil temperature to the bearings. Valves, orifices and other methods are used to ensure the proper amount of oil is applied.
In a ring-oiled bearing system, the oil reservoir is often self-contained within the bearing unit. Oil circulation is created by a ring that rides on and turns with the journal. As the ring rotates, it pulls oil from the reservoir. Oil is removed from the ring at the point of contact with the journal and is distributed via oil grooving. The oil ring acts as the pump for the oil. Oil is typically cooled via airflow over the motor; however, additional cooling may be required. In these circumstances, water cooling coils can be used to maintain proper operating temperatures.
An oil ring is designed to be one to two times larger than the shaft it is riding on. This will allow for proper rotational speed of the ring relative to the shaft speed. At this ratio, adequate oil is deposited for transmission across the bearing surfaces. Bearings longer than eight inches should be equipped with two or more rings to ensure proper deposition of oil. The oil level in the reservoir should be noted by a sight glass on the exterior of the housing. Minimum and maximum fill levels should be noted. With the proper diameter and oil level, the ring should dip one quarter or less into the oil. This will ensure the ring will continue to rotate and deposit oil at the proper rate. If the oil level is too low, an inadequate supply of oil will be delivered and impacting can occur. This will create excessive heat buildup and could cause particulate matter to enter the oil. If this occurs, the rate of failure will exponentially increase. The ring will not be able to rotate if the oil level is too high, resulting in premature failure. Drag due to incorrect oil viscosity can also cause premature failure. When the level is too high, or the viscosity is incorrect, the ring will hang on the shaft and not rotate. This allows the rotating shaft to create an isolated wear spot that will permanently damage the ring beyond function.
A proper ring profile is also critical. The most common profiles are trapezoidal, rectangular/square or T-type. The most efficient type of oil ring is trapezoidal. The oil picked up will slide down the sides of the taper on the ring and deposit it. More oil will ride on top of a rectangular ring and a T-type ring. The misconception the T-type ring is the most efficient because of increased surface area of the ring is refuted by the fact the corner of the “T” in the ring will hold the oil on top of the legs and not deposit as much as the slopes of the trapezoidal ring. Many repair facilities often put the same design back into the system that was removed. This is generally acceptable, but if lubrication is the incoming failure mode, look to the ring profile to see if improvements can be made. If lubrication delivery and dispersal are still an issue, oil groove alteration may be necessary.
When the oil is deposited by the oil ring, it is dispersed through the low-pressure clearance zone via oil grooves. Typically, there are linear pockets along the bearing. These are typically perpendicular to the load zone of the bearing, and allow for the deposited oil to be spread for converging wedge formation. If required, additional grooves can be applied to the low-pressure zone of the bearing to guide the oil. The addition of grooving the high-pressure zone of the bearing is not recommended without finite element analysis.

Ball Bearing Ryan Ossmann is general manager at Wheeler Bearing Company, powered by Jenkins. He may be reached at ryan@wheelerbearing.com. For more information, visit wheelerbearing.com.