Stainless steel’s corrosion resistance and durability enables long-lasting process equipment, pipework, tanks and structural elements in the nuclear industry. However, fabricators may find themselves facing a procurement challenge due to special requirements.
Above: The nuclear industry uses stainless steel with tight control over minor trace elements, such as cobalt Stainless Steel Sheet Distributors
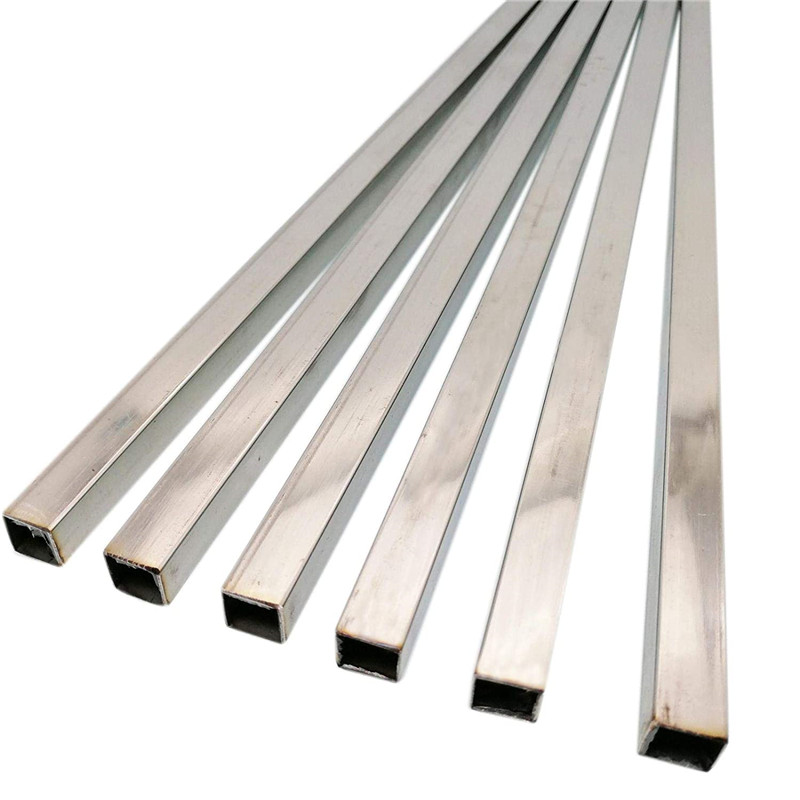
The majority of stainless steels used in the nuclear industry are based on well-established commercial grades that are widely available. However, it’s not always simple to secure material when ordering stainless steel for components in critical nuclear applications, for example where there is contact with the primary coolant.
Austenitic stainless steels are typically used in these applications. These steels contain 8 to 10% nickel to give the steel the correct microstructure and mechanical properties. However, the drawback is that nickel ores often contain trace quantities of cobalt that cannot be easily separated, so commercial stainless steels containing nickel normally also contain a trace quantity of cobalt. When exposed to radiation, this cobalt transmutes into a radioactive isotope that accumulates over time, steadily raising the health and safety risk. To avoid this the industry uses stainless steel produced to exacting standards with tight control over even minor trace elements such as cobalt. This requires the use of nickel ores obtained from mines with naturally low levels of cobalt. In addition, individual nuclear projects may have specifications covering other trace elements such as boron, tantalum and phosphorus.
Although producing low-cobalt stainless steel for the nuclear industry is technically viable, it is more costly as it disrupts a mill’s normal production. Modern mills in Europe and the USA produce stainless steel by remelting scrap in an electric arc furnace, for example Outokumpu uses around 94% scrap. This aligns with society’s drive towards the circular economy and away from use of virgin raw materials. It also cuts the carbon footprint as remelting scrap requires less energy than processing ore. However, trace elements in scrap make it unsuitable for nuclear projects. Therefore, a steel mill must incur additional costs by switching temporarily to ore-based production and purchasing specialist low-cobalt nickel ore.
For most industries stainless steel is specified by grade, product form (plate, sheet, pipe etc) and size. Many nuclear engineers also define the maximum level of cobalt and other elements. This combination of technical specifications covering cobalt content, alloy and product form vary widely between projects.
As a heavily regulated industry, only a few grades of stainless steel are permissible under nuclear codes in critical areas. In the US ASME system, these include grades 304 and 316, together with low-carbon “L” versions; similar steels exist in European standards and the French RCC-M code. Duplex grades are sometimes used where high strength is needed.
When it comes to technical specifications, the percentage content of cobalt and other trace elements varies between different plant designs and the component location within the plant. French RCC-M standards typically set a maximum of 0.20% of cobalt, but lower contents of 0.10 or 0.05% can also be requested.
Another requirement is the stringent qualification requirements set by nuclear authorities. These mean that production can only take place at steel mills with proven experience under agreed production methods and the correct quality certifications to ensure production standards, material traceability and nuclear safety culture are followed to the letter.
A final complicating factor is that engineering, procurement and construction (EPC) contractors need to order material in multiple product forms and sizes. These include heavy plate for large tanks and heat exchangers, thin sheet for small process vessels or to line cooling ponds, and tubes and fittings in a variety of sizes for pipework.
Combining these project-specific technical requirements can mean a batch of steel is tailored to one specific project.
This can create a major procurement challenge, especially as the low-cobalt requirement is almost unique to the nuclear industry and its influence is larger than it seems at first glance. The difficulties are even more apparent in smaller projects, such as repairs or replacement of components in existing plants but can also be present in new build plant if an individual fabricator is procuring material for a small part of an overall package of work.
When it comes to ordering material, a fabricator may need to procure 5, 10 or 20 tonnes of 316L material spread across several product forms such as plate, sheet and tube. However, bulk steelmaking typically produces material in melt quantities of around 50-100 tonnes.
With this in mind, an order of, for example, 20 tonnes of grade 316L with less than 0.2% cobalt, creates a set of commercial choices for the steelmaker. They could produce a full 80 tonne melt of specialist low cobalt steel to satisfy the 20 tonne requirement. However, there’s no guarantee of further orders for the same grade with the same trace element content. This may leave the balance of 60 tonnes in stock for years, tying up cashflow.
Meanwhile, the next nuclear industry order may be for 10 or 15 tonnes of grade 304 with a cobalt level that is much lower at 0.05%, and with different overall technical requirements. It’s unlikely that this second project will be able to waive their standards to accept the product that is available – instead, it will require a new large production batch of steel.
This wide variation of project requirements means that requests for small quantities are something that steel mills need to evaluate with care. As a result, EPC contractors and fabricators may find it challenging to secure material at a reasonable cost for one-off smaller nuclear projects or refurbishment work.
The tighter the specifications covering trace elements, alloying content and technical demands, the more costly the steel melt. Ultimately the cost of producing a full batch of specialist steel is likely to be borne by the ordering project. It is therefore in the interest of the whole supply chain that this batch of material is utilised fully by the project.
An underlying factor in this supply challenge is that steel mills are often perceived as commodity suppliers. Even though nuclear projects are planned and developed over years, stainless steel producers rarely get advance knowledge of the material specifications or oversight of the sizes and quantities required. Oversight of a project to aggregate together requirements to match steel production batch sizes where possible can significantly reduce costs. Earlier knowledge of the technical specifications, sizes and quantities, as well as certainty over timescales would also enable the supply chain to plan more strategically, and with that would come cost and project programme benefits.
Looking to the future, the development of small modular reactors (SMRs) could alleviate some of the challenges. Establishing serial production of modules should create more predictable ongoing demand for these specialist steels, giving steel mills and distribution companies the confidence to schedule regular production.
While many of the stainless steels used in the SMR modules are likely to be the same grades of 304, 316 and their variants that are used in standard reactors, small and micro modular reactors may also require other types of stainless steel for the balance of plant.
For example, stainless steels will be required for the thermal energy storage systems that will meet varying demand while the reactor delivers constant baseline output. Molten salt energy storage has potential as a scalable solution that is established in Concentrated Solar Power (CSP) plants. These store energy in tanks of molten salt, built from established stainless steels such as Therma 347H, although alternative grades with improved high temperature properties are under development.
Duplex stainless steels also hold promise for some applications. The grade LDX2101 has twice the strength and similar corrosion resistance to 316L. It has been used to produce steel-concrete sandwich panels in mechanical equipment modules for the AP1000 plant design, for instance.
The duplex family of grades is well suited to structural applications in the modular reactors that are being evaluated for remote communities and industrial facilities. These will need to work semi-autonomously with little operator intervention for maintenance and repair of corrosion of process equipment or structural elements.
Duplex grades are also widely used in offshore oil and gas, pressure vessels and large storage tanks. They have recently been adopted to build bridges with a design life of 120 years that can avoid costly road and railway closures – a philosophy that could also bring long-term cost and operational benefits to the emerging SMR sector.
As a material, stainless steel has an important role to play in ensuring a long and safe operating life for nuclear reactors. When specifying the material, it’s worth knowing that the unique requirements of the industry might make it challenging to secure material. Therefore, it’s worth thinking ahead to discuss plans in advance with material producers to ensure material will be available in the right specification when it’s needed.

Stainless Steel Compared To Steel Author: Andy Backhouse, Lead Technical Manager, Outokumpu