Michael Feechan Chris Makselon Stephen Nolet Fiberspar Corp.
Early development of composite coiled tubing centered on downhole applications as a low fatigue and corrosion resistant alternative to steel coiled tubing (CT). After this initial development period, market pull re-focused the technology on surface applications. Aluminum Coiled Tube
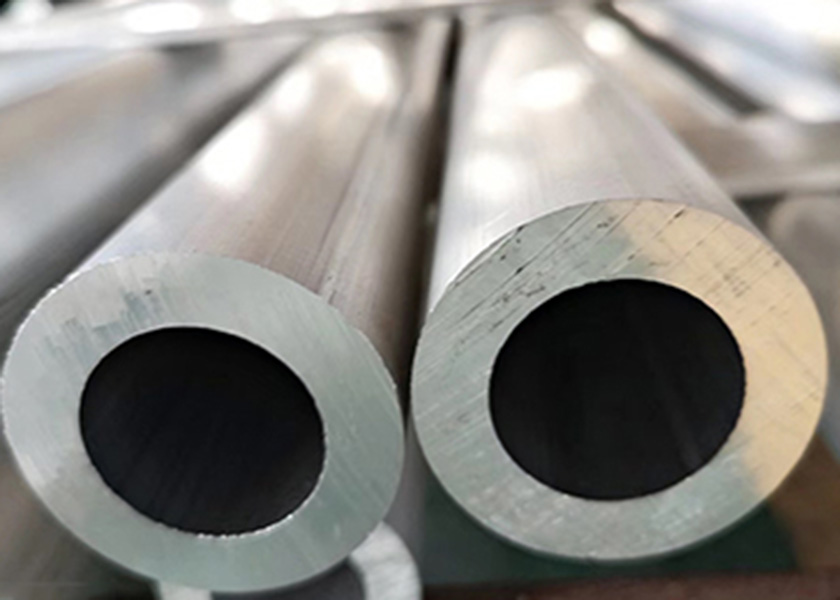
The basic design of the spoolable composite tubing consists of an internal fluid barrier, normally a thermoplastic extrusion, on which the reinforcement is wound in a continuous process.As a result, the technology was first commercialized in 1999 as LinePipe for surface gathering and injection applications. Almost 2 million ft of LinePipe has been manufactured and installed in surface applications, mostly in North America.
The technology has proven to be a reliable and cost effective alternative, particularly for a corrosive application. It has enabled innovative installation techniques that are rapid, safe, and require little manpower, and it is setting new standards in installation speed and reliability for the small diameter pipe construction industry. Momentum is gathering as operating companies realize the benefits in installation and performance. Composite spooled tubing has become a realistic alternative to existing corrosion resistant solutions, such as lined steel and discrete length reinforced fiberglass pipe. The range of applications is growing as the technology mat-ures and develops.
The product is routinely made in lengths of 18,000 ft, and occasionally longer, in a highly automated 24-hour continuous process.
The basic design of spoolable composite tubing consists of an internal fluid barrier – normally a thermoplastic extrusion, on which the reinforcement is wound in a continuous process. The reinforcing laminate consists of multiple, counter-wound fiber layers, normally glass or carbon, or a hybrid of both, in an epoxy matrix. The pipe is cured in a tunnel oven and the finished pipe wound onto spools.
A proprietary process ensures that the liner is chemically bonded to the structural reinforcement for the life of the product. The process involves tight control of relatively small, but well-defined process windows. All LinePipes, and most designs of pipe for downhole, use a fiber geometry that allows spooling at a maximum 3.5% strain, equivalent to a drum diameter of 28 times the outside diameter of the pipe. These spooling strains and low unit weight, coupled with specially designed trailers, allow larger sizes and quantities to be transported than with steel CT. While the basic construction remains the same, many variations on the design can be engineered and produced on the same process line for specific applications such as:
While not the top priority over the last three years, some development of the technology for downhole applications has continued. The surface applications are reaching a point of maturity that will allow additional focus on the downhole market. Although the technology for use in surface and downhole applications is broadly similar, several changes have been implemented to make the pipe suitable for these applications.
Downhole applications include permanent installations, such as production tubing, velocity strings, and injection strings, particularly for corrosive environments, and service work such as CT intervention and drilling.
Well intervention describes the range of work undertaken to improve the production from a well, including cleanouts, acidizing, and other processes. Coiled tubing has been the method of choice for these operations for many years. Some of the earliest designs of composite CT were aimed at this market. Intervention operations across a range of well types produce demanding specifications. As a result, all first-generation development of CT designs used carbon fiber reinforcement in a multi layer, variable geometry laminate. This configuration optimized axial performance and fatigue life, while preserving reasonable spoolability. Although these designs had the downside of being inherently high cost and presented several manufacturing challenges, the performance proved to meet most requirements. In 1998, a 6,500-ft-long 1 1/2-in. diameter CT string in this design was built and deployed.
The pipe performed well, but it offered no obvious commercial advantages over small diameter steel CT. The trial was intended to provide some field experience, and assist the further development of the technology. This experience has been applied to larger diameter strings required for drilling. After initial application testing, the use of the 1 1/2-in. CT string was discontinued while development efforts focused on SmartPipe for an advanced coiled tubing drilling system.
Over the past seven years, Fiberspar has developed continuous spoolable composite tubing technology, building upon work done by Conoco in the previous five years.
In 1998, Fiberspar was commissioned to design and construct composite CT with conductors for real-time power and data transmission for an advanced coiled tubing drilling system. A scaled-up version of the first-generation coiled tubing design was developed including carbon reinforcement and embedded conductors. The pipe was 2 7/8-in. diameter, had a 7,500-psi pressure rating, was extensively tested, and was then run in two real drilling situations (test wells). There were several design iterations, and the pipe ultimately met all the required performance specifications. Highlights from the development of this pipe included:
In 2002, a new CT prototype design was tested. It was built around construction techniques, fiber geometries, and materials similar to the now successful LinePipe designs, and a significant departure from both the designs used in the early products and those used in the SmartPipe. This design resulted in much lower costs, around 1.5 times to 2 times steel CT equivalent, compared to 4 or 5 times with original designs. The fiber geometry also provides enhanced spoolability, allowing longer lengths on smaller spools, while preserving much of the performance of the previous designs.
A 6,500-foot, 1 1/2-in. string of this design was built and deployed in late 2002, where it has been used on P&A work. While P&A work is a relatively benign operation, it is rapid and repetitive and offers the best opportunity to see the string run frequently over a short time period. An average of nearly one well per day was completed during the first month of operation, and the string was still in good condition. This begins to validate the expectation of extended working life for composite CT strings compared to their steel counterparts.
Work has also continued on higher performance versions of the intervention string aimed at more advanced work such as CT fracturing and pumping of aggressive fluids such as hydrogen peroxide and Xylene. This has included innovative hybrid designs with variable fiber geometries, multiple reinforcing materials, and externally bonded jackets using engineering thermoplastics such as polyphenylene sulfide (PPS). A 1 1/2-in. prototype incorporating many of these developments has been manufactured and will be deployed for field testing in 3Q 2003.
The performance parameters required by the advanced SmartDrilling system resulted in a high-performance but high-cost tubing design. It was clear that it would not be cost-competitive with standard steel coiled tubing for more conventional work. Customer information indicated that the CT drilling industry had a need for larger diameter pipe to extend performance, and that 3 1/2-in., 4-in., or 4 1/2-in. steel CT was difficult to handle and transport.
Drawing on knowledge gained from both LinePipe experience and well intervention products, a lower-cost glass fiber-reinforced 3 1/2-in. CT design was developed, manufactured, tested, and run in drilling operations. The pipe showed excellent fatigue life, while being spooled to 3.5% spooling strains. Costs in production of such a string are estimated at 1.5 to 2 times the cost of same-sized steel CT.
After some early problems with mechanical equipment interaction, which were resolved by stricter control of equipment settings, this pipe design was used to successfully drill 16 wells. The tests were discontinued for commercial reasons, but judged to be a success because the composite CT appeared to be in excellent condition and maintained full pressure integrity. The program will be resumed this year. A 4-in. design has been manufactured and will be run in the next few months.
Permanent downhole installations include velocity strings, injection strings, production tubing, and casing. Corrosion is a common problem in a high proportion of wells, and composite coiled tubing is potentially an attractive solution because it combines the advantages of a fast-deployed coiled tubing product with corrosion resistance. Permanent installations potentially use very high pipe volumes and are probably the most attractive applications. Two permanent downhole installations have been completed.
In 1998, 2 3/8-in. outside diameter composite tailpipe extensions were installed in three gas wells in the southern North Sea. The installations were completed rapidly, and initially the wells performed satisfactorily. After a period ranging from a few months to one year, however, all of the wells stopped producing. Subsequent investigation showed that the tailpipes were installed in the producing zone at temperatures in excess of 200° F. Results from simulated laboratory testing of the resin system used in these extensions showed substantial degradation after lengthy exposure at these temperatures. The use of this epoxy resin has been limited to 150° F. Since then, a new epoxy resin suitable for 180° F operation has been introduced. Development of cost effective alternative resin systems for higher temperature applications continue to be the focus of much effort.
Following the lessons learned from this installation, a 1 1/2-in. CT string was installed as a heater string in Canada in 1999. Heater strings inject hot water into the well annulus to prevent formation of hydrates. The string has been in use for over three years and continues to operate normally.
CT technology has many advantages, the primary one being the low cost of deployment in many downhole applications. While advances continue to be made in performance of steel CT and new applications continually introduced, there are some inherent limitations, such as fatigue life, difficult handling of larger sizes, and corrosion, that present commercial or technical hurdles. It was envisioned that composite CT would overcome many of these disadvantages and allow the range of applications for CT to grow.
Careful choice of application and attention to application design are important if the advantages are to produce cost benefits. The current strategy is to focus on areas where one or more of the attributes of light-weight, corrosion resistance, and fast deployment methods have commercial advantage and to select applications well within the limitations of the materials – shallow, low-temperature, low-pressure applications – to allow commercial success.
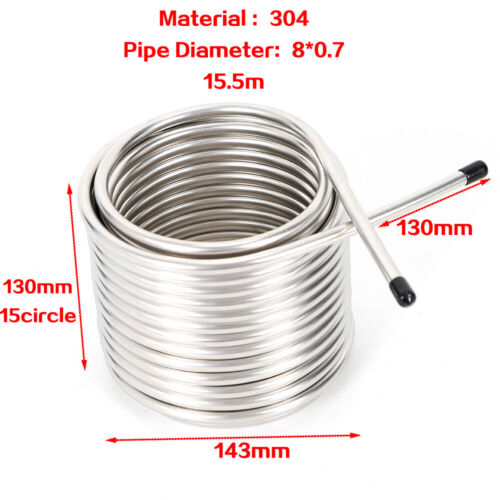
Coiled Tubing Downhole Tools While technology continues to develop for general downhole use, the focus is on permanent installations where several applications show promise and are being actively pursued. These include: