Fashion is among the most environmentally damaging industries globally, contributing to water pollution through dyeing processes and generating immense amounts of textile waste. Garments are often shipped all over the world, significantly contributing to carbon emissions.
Ganit Goldstein SM ’23, a Jerusalem-born designer who recently completed a master of science in architecture studies in computation at MIT, has spent years exploring alternatives to standard production methods and workflows. Combining traditional craftsmanship with cutting-edge technologies, the former research assistant at the Self-Assembly Lab, and 2023 MIT Morningside Academy for Design (MAD) Fellow, is blazing a trail forward. Material Printed
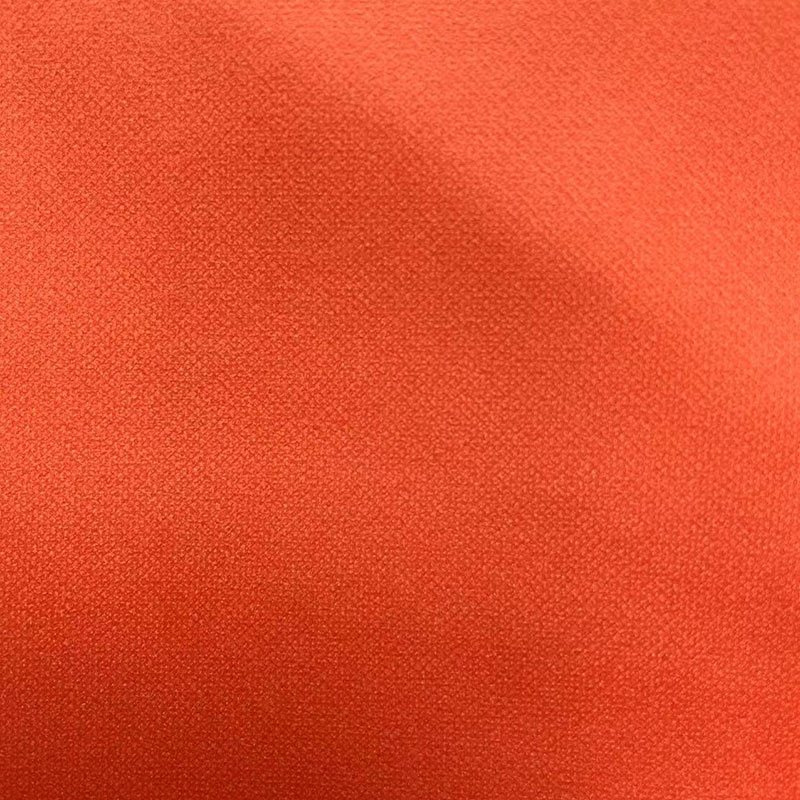
Recalling her lifelong affinity for textiles and sewing, Goldstein shares: “I was always sewing my own clothes. But I marveled at new technologies when I used to visit my brother, who used to work for Intel. I loved to see the new gear available in his office.”
After her military service and an experience as an officer in the Israeli Navy, Goldstein pursued a bachelor's degree in fashion and jewelry design. During that time, her fascination with technology led her to explore architecture departments, where 3D printing equipment was available. Goldstein started asking herself pivotal questions: “Could we print garments? What would be the benefit of using new technologies alongside craftsmanship in the fashion world?”
During an exchange student program in Tokyo, Japan, she acquired ancient textile craft techniques, such as Ikat weaving, that are still perceptible in her most recent designs. Her expertise in textiles, from past to present, led her to develop along the years garment collections that hybridize new technologies such as 3D printing and scanning with traditional methods of Ikat weaving and dyeing techniques.
Goldstein’s talent and dedication earned her a scholarship to study at The Royal College of Art in London, where she delved into a world of new techniques, materials, and processes. There, she discovered embedded electronics and explored the use of natural materials like seaweed and organic matter. Her final project, “Rhythm of Matter,” established a methodology to produce large-scale embroidery patterns with conductive thread and virtual reality application to rethink how fabrics can be an interactive tool, set both as digital and physical artifacts.
In her quest to re-imagine the potential of overlooked or underutilized materials while finding ways to reduce the industry’s impact on the planet, Goldstein leaned further into experimenting with 3D body scans and digital designs, to create garments not only aesthetically striking, but environmentally conscious. Goldstein quickly understood that revolutionizing the way clothes are created requires studying the entire workflow: conception, production, logistics, retail.
While further developing a distinctive style at the intersection of tradition and technical innovation, Goldstein introduced a new concept at the heart of her work: customization. She saw how this could allow individuals to have garments tailored specifically to their bodies and needs. By incorporating 3D scanning, motion tracking, and other innovative techniques into the manufacturing process, Goldstein’s research could minimize waste, improve garment fit and durability, mitigate climate impact from logistics, and ultimately transform the retail experience, avoiding frequent returns. In a world grappling with environmental challenges, this approach holds immense potential for the fashion industry.
One of Goldstein’s most cherished designs is a kimono made from a new 3D-printed fabric, constructed without any seams. This project, for which she received a 55,000-euro grant, was part of the Horizon 2020 EU funding program, connecting designers and industry leaders in the textile world to re-think the way garments can be produced in the near future. With approximately 20 puzzle-like fabric pieces which integrated embroidery within the printing process, assembled seamlessly, Goldstein demonstrated the possibilities of transitioning from a digitized design to a tangible, manufactured end-product.
During her time at MIT, Goldstein pushed the boundaries of her previous works by mobilizing a number of resources available to her. Her multiple collaborations seem to have further enhanced her design journey and elevated her versatility as a designer. In addition to joining the computation groups, she took a synthetic biology course, which led her to discover new biomaterials and natural dyeing techniques with interactive properties, such as changing color with heating. As part of the Self-Assembly Lab, she applied her knowledge to the prototyping of a new kind of spacesuit sleeve — a compression-based garment concept in collaboration with Professor Dava Newman’s research group.
With MIT.nano, she collaborated with experts in motion-tracking technology, a field seldom used in garment production (it is traditionally used in filmmaking, gaming, or virtual reality). At MITdesignX, she partnered with other researchers to develop the business aspect of her customization proposals, particularly focusing on shoes for toddlers that can grow with kids, using special fiber and knitting technologies. As part of the MIT Morningside Academy for Design fellowship program, she had the opportunity to explore freely in a multidisciplinary environment providing learning and financial support.
Recently, Goldstein shared feeling particularly inspired by extreme environments, where she contemplates how fabrics can be imbued with technology and special properties to support and empower individuals in challenging conditions. Whether it's creating garments with embedded data for motion tracking, temperature regulation, or personalized measurements, her work aims to provide functional solutions and a second skin when needed.
As part of her thesis, Goldstein presented in May the prototype of a 60-piece spacesuit, featuring a gradient map of colors translating body scan and motion tracking data into specific material properties. This visually striking ensemble uses polymers, directly 3D-printed on the surface of the fabric, applying mechanical pressure instead of gas pressure on the body. This allows for more flexibility, comfort, and mobility. This project not only explores future generations of mechanical counterpressure (MCP) spacesuit designs, but also proposes a potential workflow for customized garment manufacturing.
Reflecting on her experience at MIT, Goldstein expresses the profound impact on her perception of design and its value: “It's been a completely free environment to explore without boundaries. I have been able to establish a design language that merges engineering and technology in a meaningful way. For me, MIT MAD is a reflection of how the future of design enhances creativity through an interdisciplinary environment. Building this community has been such a valuable experience. There has truly been connections, collaborations, and the sharing of knowledge every step of the way.”
At the intersection of fashion, engineering, and technology, Goldstein’s work highlights the potential of collaboration between different fields to achieve tangible and sustainable results. With a vision focused on customization, waste reduction, and the seamless integration of technology, she represents a new wave of designers devoted to transforming the industry. Her dedication to finding balance between technology, sustainability, and aesthetics demonstrates her commitment to transform design as we know it.
This website is managed by the MIT News Office, part of the Institute Office of Communications.
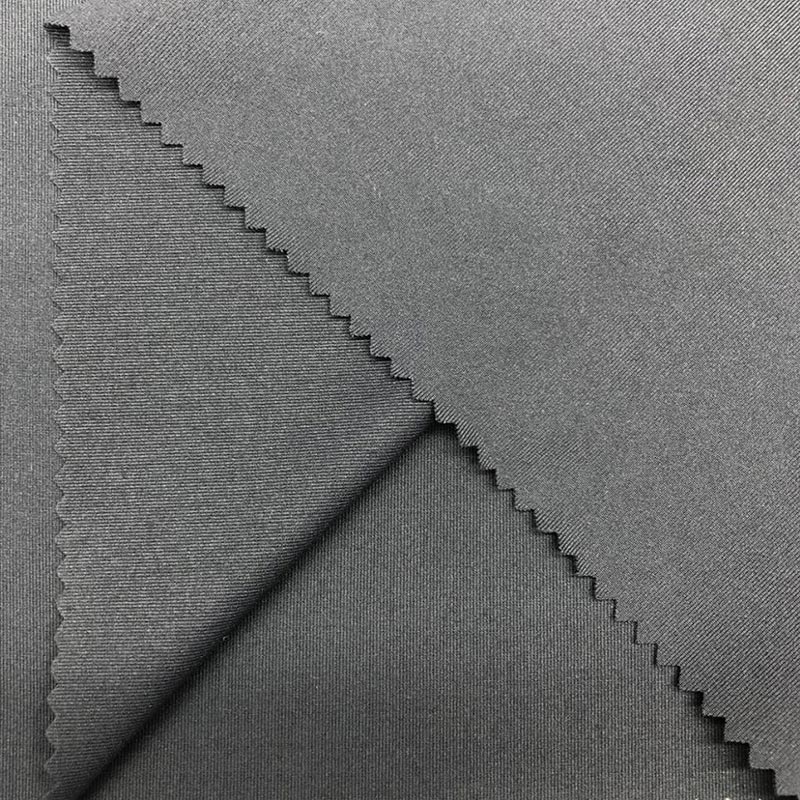
Polyester Swimwear Fabric Massachusetts Institute of Technology 77 Massachusetts Avenue, Cambridge, MA, USA