Tom Rayeck reveals how the combination of optimised carbide grades, AM and conventional manufacturing leads to durable valve components
Flow control is crucial within the oil and gas industry. Therefore, choke valves in numerous variations and dimensions are essential components for controlling the pressure and flow of well products. Having to endure severe conditions of multi-flow media, these components may suffer extreme mass loss by exposure to solid particle erosion and acidic corrosion. Maintaining or replacing worn-out parts is by far the least desirable option in the long term. Instead, choosing the most durable and reliable solution that easily withstands erosion as well as corrosion is preferable. Carbide Grinding Tank
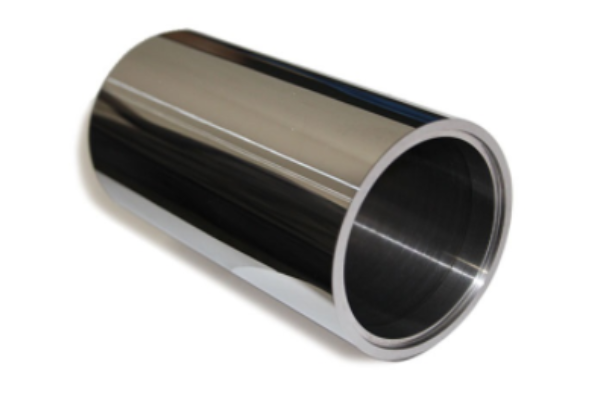
For such situations, cemented carbides have been a well-proven solution: high hardness, wear resistance and toughness, combined with other mostly adaptable, high-performance characteristics, make cemented carbide the ideal material for numerous applications. At present, Ceratizit has over 100 different carbide grades with varying compositions for specific applications available. They are optimised for erosion, corrosion, thermal fatigue resistance, optimal hardness/toughness balance or non-magnetic properties – depending on their intended use and the material combination.
Most cemented carbides use a cobalt binder phase. But due to their limited corrosion resistance and their being prone to binder leaching, pure WC-Co carbides are often not suitable for application fields where corrosion is likely to occur. The only solution is to use materials such as Co/Cr, Co/Ni or Ni/Cr rather than pure cobalt binders. These grades, such as Ceratizit’s ultrafine nickel-binder grade CTU17R, have almost the same characteristics as WC-Co (hardness, dimensional stability, high resistance to wear and tear), but with one significant difference: they offer greatly improved resistance to corrosion and abrasion.
Now imagine the proven reliability of these carbide grades combined with the freedom of valve design offered by additive manufacturing (AM). The role of AM is still on the rise, either as a complementary technology to existing manufacturing processes, or even being accepted as a fully fledged alternative. Whereas 3D printing in the past was mainly used for plastic materials, more and more metal-based printing applications can be found today.
Nonetheless tungsten carbide 3D printing is still very exotic and is practised only by very few companies. Ceratizit is one of these companies and is now also able to offer its proven grade CTU17R as an AM variant. That opens up many opportunities for the design of components for the oil and gas industry, especially those that are impossible to achieve by conventional production processes.
3D printing offers a number of advantages when compared with legacy processes. The most important of these is the added flexibility 3D printing allows in design terms. 3D printing can make components that are hollow in certain areas. How is this possible? In 3D printing, material is added in layers, so the material density of the core can be altered. That means that certain areas can be hollowed out when required while other more critical areas can be reinforced – an ideal basis for lightweight design with increased strength. 3D printing also helps to save carbide, as production becomes more material-efficient. The technology can produce components that are smaller in terms of volume, but still yield the same performance.
But when it comes to extraordinary dimensions, such as valves with diameters of more than 400mm or lengths in excess of 300mm, traditional production processes are back in the game. For example, horizontal flow valves can be equipped with carbide inserts to regulate the pressure and therefore the flow of oil, gas or some other medium. The real challenge in production is to deliver the desired dimensions in spite of the deformation that occurs in the sintering process. Every component has a linear shrinkage of 21 to 25% after sintering, and needs some subsequent grinding to get the exact final geometry the customer needs. Not forgetting that we start with a pressed blank weighing 300+kg and reduce it to something between 80 and 120kg for the final part. It requires very distinctive and specialised machinery, as well as a great deal of expertise, to produce parts for the oil and gas industry that will last and withstand the harshest conditions.
Tom Rayeck is with Ceratizit

Tungsten Carbide Drill Bits © Setform Limited 2019-2024 | Privacy policy | Archive