Cam followers convert rotary to linear motion and range from simple two-dimensional cams to complex three-dimensional indexing cams with several followers. In linear-motion applications, cam followers support lateral or vertical travel, such as rollers for platform support and die transfer. In any application, cam follower bearings reduce sliding friction and wear on the cam and track, which lets it maintain its precision. Overall, the choice of which type of bearing is used affects the cam follower’s performance.
There are three types of cam followers: standard stud, heavy stud and yoke. Stud types are mounted cantilever-style in a support housing. Heavy stud versions are for heavy loads, shock loading and applications requiring minimal deflection. Except for the stud diameter and end plate design, standard and heavy stud versions are virtually identical. loose needle bearings rollers
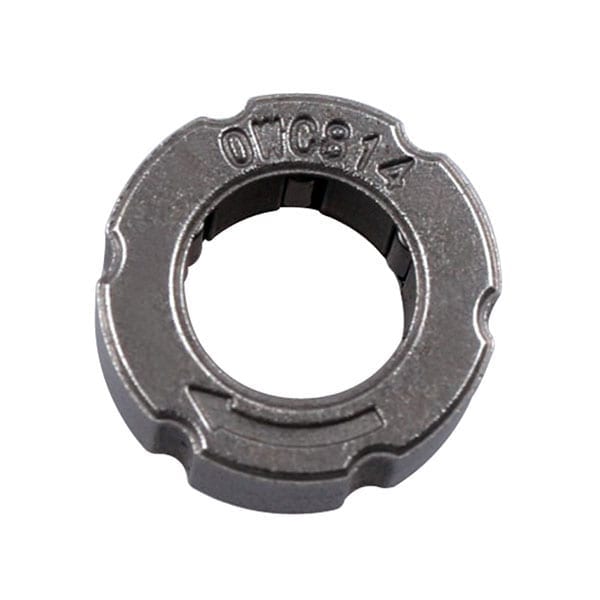
The yoke version mounts on a pin with a straddle or yoke support. Yoke mounting distributes loads more uniformly over the bearing, so the working load limit for yoke-type followers are generally equal to that of heavy stud followers.
Most cam follower bearings contain needle rolling elements. These bearings are well suited for supporting radial loads but not thrust loads. An alternative to standard needle rollers is a double row of cylindrical roller elements. The rollers have larger diameters than needle-roller cam followers of the same size. Thus, cylindrical rollers typically provide higher radial load ratings and can support a light thrust load along with the radial load.
Another type of track roller bearing consists of deep-groove ball bearings or tapered roller bearing assemblies. Units with ball bearings or tapered roller bearings support radial and thrust loads, and in certain applications can support pure thrust load. Such units typically have ball bearings for rolling diameters less than 3 in. and tapered roller bearings for rolling diameters 3 in. and larger. These track roller bearings have large lubricant reservoirs and are sealed, so they can operate in dirty environments without lubrication maintenance.
Track roller bearings also come with several different roller profiles (flanged, V-groove, cylindrical), letting them ride on different types of tracks or perform multiple functions. Cylindrical rollers operate on flat tracks. Flanged and V-shaped rollers maintain an maintain position on a rail or edge. V-rollers also operate on special “V” tracks, square or round bars, and sometimes angle-iron tracks.
Most cam followers can be equipped with some or all of the following options to meet a specific application’s needs.
Seals extend bearing life by keeping contaminants out and lubricants in. The seals of a needle roller cam follower are typically made of a nylon. It fits on the end plate or flange OD and provides a close-running, labyrinth-sealing effect with the outer ring. Some manufacturers include a back plate that reduces friction between the bearing’s outer ring and the respective end plate or flange. The plate separates these adjacent faces, so metal-to-metal sliding contact is eliminated.
The resulting lower operating temperature extends the life of the lubricant and makes higher operating speeds possible.
Some double-row cylindrical-roller cam followers use a rubber lip seal. This seal is effective at retaining lubricant and excluding contaminants. In many cases, it needs no relubing.
Crowned OD on the cam follower roller surface compensates for small misalignments between the cam follower and the cam or track. This helps prevent corner loading on the roller and reduces thrust loads on the bearing. Crowned OD also reduce thrust loading in applications involving rotary or circular motion, such as turntable supports.
Hex holes in either the roller or stud end of the bearing accommodates a standard hex-head wrench, which has more holding power. Stud-type bearings are usually supplied with only a screwdriver slot, which lets technicians hold the stud while tightening the mounting nuts.
Eccentric stud bearings let technicians adjust the radial position of the bearing relative to its support housing. This is most useful when several cam follower bearings support a load and mounting inaccuracies prevent standard bearings from equally sharing the load. The eccentric adjustment feature can also compensate for cam or track wear.
Caged rollers on some needle-roller type cam followers (typically in metric series) may be used in applications requiring higher speeds or longer pre-lubricated life. It reduces internal friction and provides a larger grease reservoir than conventional full-complement needle bearings. However, the load rating is lower compared to the full-complement design, as there are fewer and shorter rolling elements.
Self-lubricating bushings from some manufacturers are well-suited for lower-speed applications and where relubrication is undesirable. They use a metal or polymer bushing to replace the needle rollers used in standard bearings. The bushing’s life depends on the amount of internal wear acceptable in a specific application. Although this type is generally suited for no lubrication maintenance, when feasible, an intermittent oil supply can extend bushing life.
To select the right cam follower bearing for a cam or track system, consider the load magnitude and type, speed, deflection, misalignment and lubrication.
Loads, speeds and life requirements. Load magnitude and direction affect the bearing type and size that would best. For stud cam follower bearings, the stud strength and deflection limits determine load capacity. To calculate bearing life, especially when loads vary, consult the manufacturer’s literature or website for guidance.
Applications involving combined radial and axial loads may require ball or tapered roller bearings Be wary of shock loading, which can damage the inside and outside of the bearing’s components. Depending on the load magnitude, brinelling (aka permanent deformation of races and rolling elements) can cause vibration, and higher shock loading could fracture the bearing.
Speed limits are a major factor in determining which bearing will be best. Full complement needle rollers usually have the lowest speed limit. Higher speeds are possible with caged needle bearings and sometimes cylindrical or tapered roller bearings. Ball bearing units handle the highest speeds because of their low internal friction. Consult the manufacturer on speed limits for specific applications.
Misalignments and deflections. Crowned rollers reduce the stresses caused by angular misalignments between cam followers and cams, but they require increasing the track capacity by about 20% to accommodate the smaller contact area and resulting higher contact stresses.
Cantilever-mounted studs deflect under load. Factors that affect the amount of deflection include the corner radius in the stud support housing, the fit between support housing and stud (see drawing below), and the housing material. To reduce this deflection, consider using a heavy stud or yoke-mounted unit. For applications with deflections and subsequent thrust loading beyond the capability of a needle bearing, use cylindrical rollers, ball bearings or tapered roller bearings to handle the thrust loading.
Lubrication. Oil is the preferred lubricant in higher-speed cam applications because it cools bearings more effectively and does not deteriorate as quickly as grease. Oil is usually applied to bearings by the splash method. Grease is suitable for slower-speed cam and track applications. Most stud type cam followers are supplied by the factory prepacked with grease. For stud type cam followers, grease maintenance can be applied via axial and radial lubrication holes in the stud. For yoke type bearings, apply grease through the mounting pin.
The oil, or oil carried by the grease, should have a viscosity of 20 cSt at the bearing’s operating temperature. Speed is the major influence on operating temperature but loading also affects it. To estimate operating temperature, compare actual speeds and loads to the manufacturer’s limiting speed and dynamic load rating. Temperature limits for general purpose greases usually range from 225 to 250°F. For prolonged operation, it is typically better to keep the temperature at least 50°F lower.
Lubrication intervals depend on the application. Bearings exposed to extreme contamination, such as washdowns, may need daily lubrication. In clean environments, however, bearings may run a year or more before relubrication. Some cam followers cannot be relubricated, but they usually have more effective seals and large grease reservoirs.
Selecting cam or track hardness. Selecting the proper cam or track surface hardness can be as important as finding the right bearing. A cam or track that is not hard enough will wear or plastically deform under load.
When dimensional accuracy is not critical, use soft materials to reduce costs. For example, the work hardening of low-carbon steel, accompanied by small amounts of wearing of the bearing on the track surface, may be acceptable in some applications. For more precise applications, use hardened track and cam surfaces (up to 60 HRC) to minimize wear.
The capacity of a steel track, defined as the bearing load it withstands without plastically deforming its surface, depends on the bearing size and track strength and hardness. Track capacity values for specific cam followers are available from bearing manufacturers.
Cam and track surfaces are often difficult to keep lubricated; however, keeping a coating of oil or grease on these surfaces prevents excessive wear.
To promote long bearing life, make sure cam followers are properly mounted. A stud bearing requires a snug fit between the stud diameter and bore in the support housing. The bearing end plate must be backed up by the support housing face, and the housing face should be square to the housing bore. Refer to the manufacturer’s recommendations for housing fit as well as nut clamping torque. Avoid excessive tightening; it can stretch the stud and shrinks its diameter and thereby become loosened in the housing bore.
Suppose you need to mount a stud cam follower in a blind hole. A nut cannot be applied to the threads, so ensure the stud fits properly in the housing. Using a cam follower with a hex hole allows you to tighten the stud to obtain proper end plate support. A better method is to lock the stud to the housing with a pin or use setscrews bearing against the stud.
For eccentric stud bearings, the eccentric bushing must fit loosely in the housing bore so it can be adjusted. The housing must be at least 0.010 in. wider than the bushing length for proper end-wise clamping of the bearing. After adjustments are made, a mounting nut may be applied to the threads to hold the stud in place.
Yoke-type cam follower bearings also require proper end plate support; otherwise, they might work themselves off the inner ring. The preferred mounting methods permit axial clamping of the end plates (see image below). An alternate method is acceptable if yoke dimensions are controlled closely, so when the nut is tightened, the yoke has enough spring to enable full area clamping of the end plate faces.
The basic designs of cam follower bearings to distribute loads have changed little over the decades. However, manufacturers such as Regal Beloit’s McGill and others have expanded the range of offerings for specialized and heavy-duty applications, including maintenance-free, corrosion resistant and extreme-temperature designs incorporating advances in treated stainless steel and manufacturing processes. By matching the wider range of designs to specific applications with proper installation, alignment, and lubrication, today’s cam follower bearings offer better performance with longer working lives.
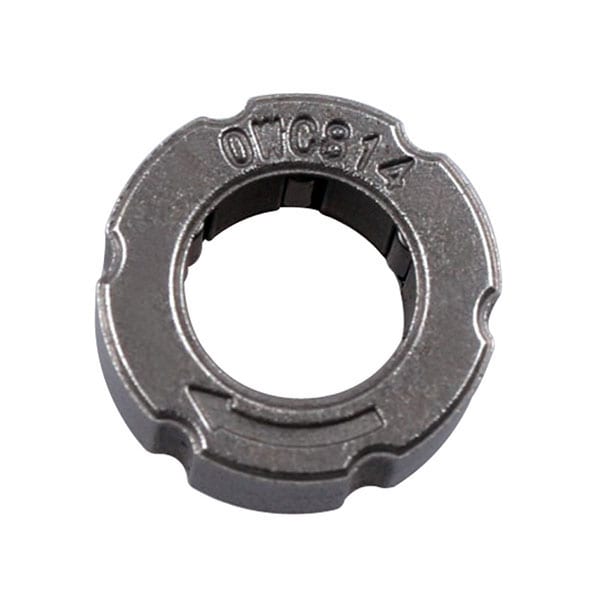
Wholesale Automotive Bearings Kevin Mues is manager of application engineering at Regal Power Solutions, a subsidiary of Regal Beloit Corp.